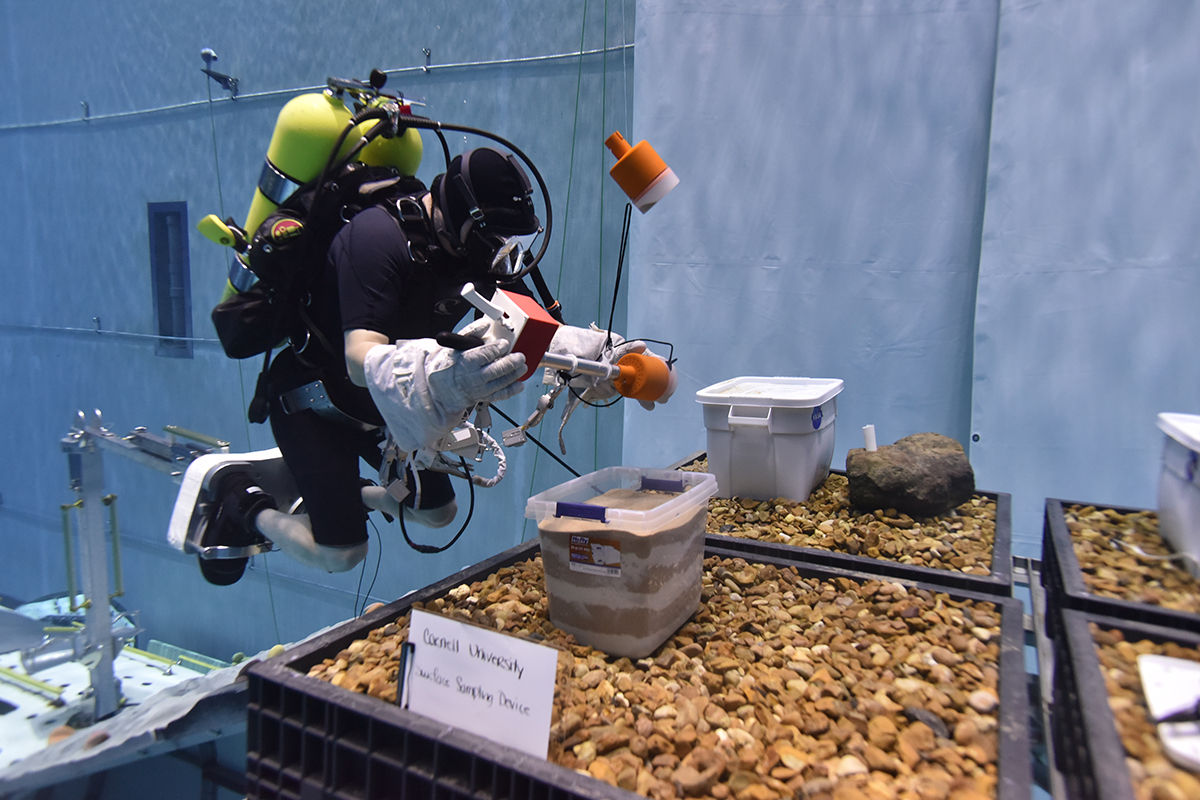
Challenge Chosen
The International Space Station (ISS) has many handrails mounted on its exterior to enable astronauts to get around during Extravehicular Activities (EVA), or spacewalks. These handrails can develop sharp edges due to impacts by Micrometeoroids and Orbital Debris (MMOD). The sharp edges can be dangerous since they have the ability to cut parts of the spacesuit, in particular the gloves. This challenge is multifaceted. First, the astronauts need to be able to detect a sharp edge, which can be difficult when wearing a pressured spacesuit. Then, once located, the astronauts need to remove or cover the sharp edge without creating an additional hazard. Design a method for both detecting sharp edges AND removing/or permanently covering sharp edges from an EVA handrail.
Micro-g Neutral Buoyancy Experiment Design Teams (Micro-g NExT) challenges undergraduate students to design, build, and test a tool or device that addresses an authentic, current space exploration challenge. The overall experience includes hands-on engineering design, test operations, and public outreach. Test operations are conducted in the simulated microgravity environment of the NASA Johnson Space Center Neutral Buoyancy Laboratory (NBL). Teams will propose design and prototyping of a tool or simulant identified by NASA engineers as necessary in space exploration missions. Professional NBL divers will test the tools and students will direct the divers from the Test Conductor Room of the NBL facility.
Micro-g NExT Competition
Assumptions
-
The location of the sharp edge is not visible to the astronaut. It has to be detected by another method.
-
The MMOD impact that creates the sharp edge will create a crater no bigger than 1/8” in diameter (Reference Figure 2).
-
The sharp edge can appear on either of the three exposed handrail faces (Reference Figure 3). It can appear on any part of the profile (reference Side view in Figure 3).
-
The astronaut is stabilized, has 2 free hands and can react small amounts of load.
-
The device can have multiple parts that can attach and detach.
Requirements
-
The device/s shall be able to detect sharp edges that protrude between 0.01” – 0.06” from the surface of the handrail.
-
The device/s shall be able to remove or permanently cover the sharp edge to the greatest extent possible.
-
The structural integrity of the handrail must not be compromised.
-
The creation of Flying Object Debris (FOD) should be minimized.
-
The system can be manual, pneumatic or electrical. If the system is pneumatic or electrical it must meet additional NBL Requirements.
-
The total weight of all parts you provide should be less than 15 lbs.
-
The device/s shall be able to pack within a 12” x 16” x 18” volume.
-
Any removable components shall have a tether attachment point 1” in diameter.
-
All tools must be operable with EVA gloved hands (like heavy ski gloves).
-
Tools must not have holes or openings which would allow/cause entrapment of fingers.
-
Tools must be made from the NBL Approved Materials List or a waiver must be granted.
-
Lubricants must be selected from the NBL Approved Lubricant List or a waiver must be granted.
-
There shall be no sharp edges on the tool.
-
Pinch points should be minimized and labeled.
-
Tools shall be designed with drain holes or geometry to allow the free flow of air and water as required to support submersion and removal to and from the NBL pool.
Test Setup
-
Each team will have at least 2 sharp edges to detect and remove.
-
A simulated sharp edge will be placed somewhere on one of 3 exposed handrail faces (reference Figure 3).
-
The test subject will use your tool to detect the sharp edge.
-
Once located, the test subject will then attempt to remove the sharp edge.
-
Confirmation the sharp edge has been removed can be done with your detection tool and/or by support divers.